How To Find Minimum Average Cost
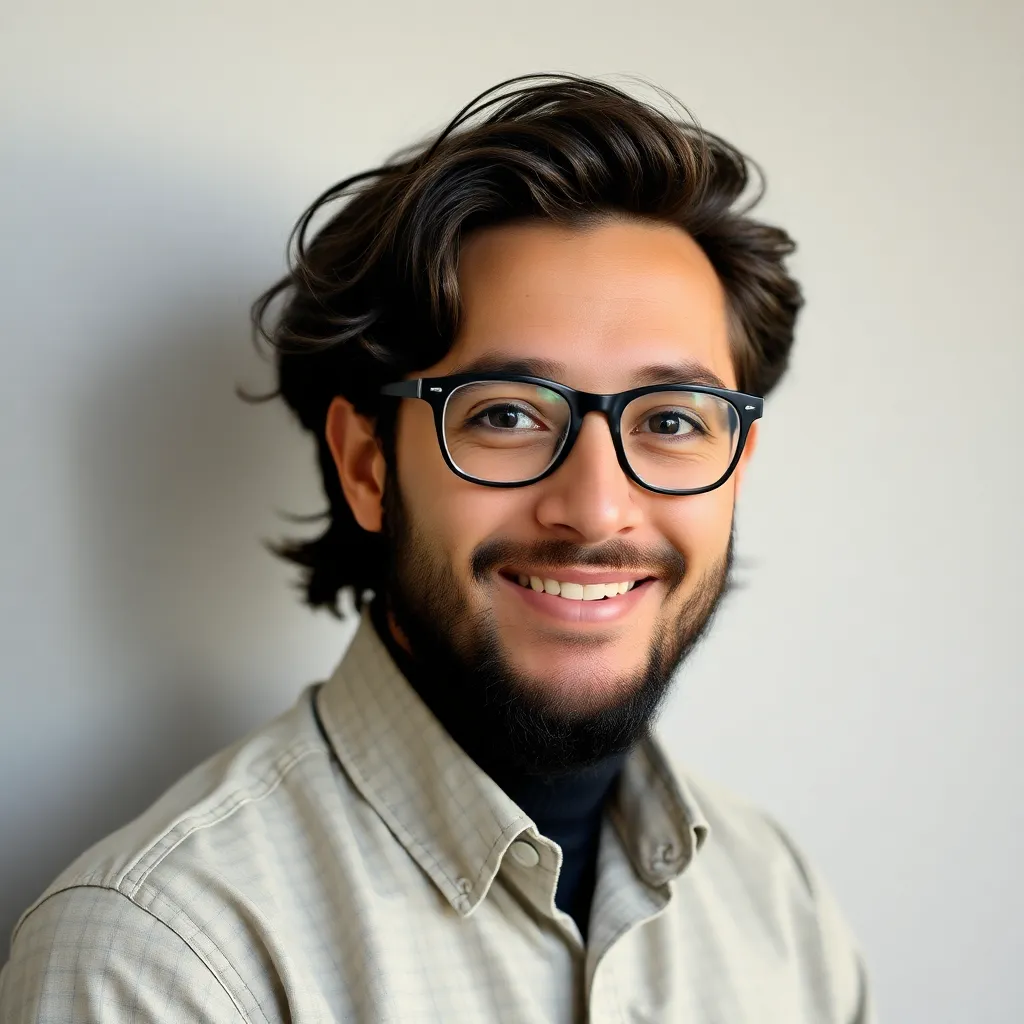
News Co
May 08, 2025 · 6 min read
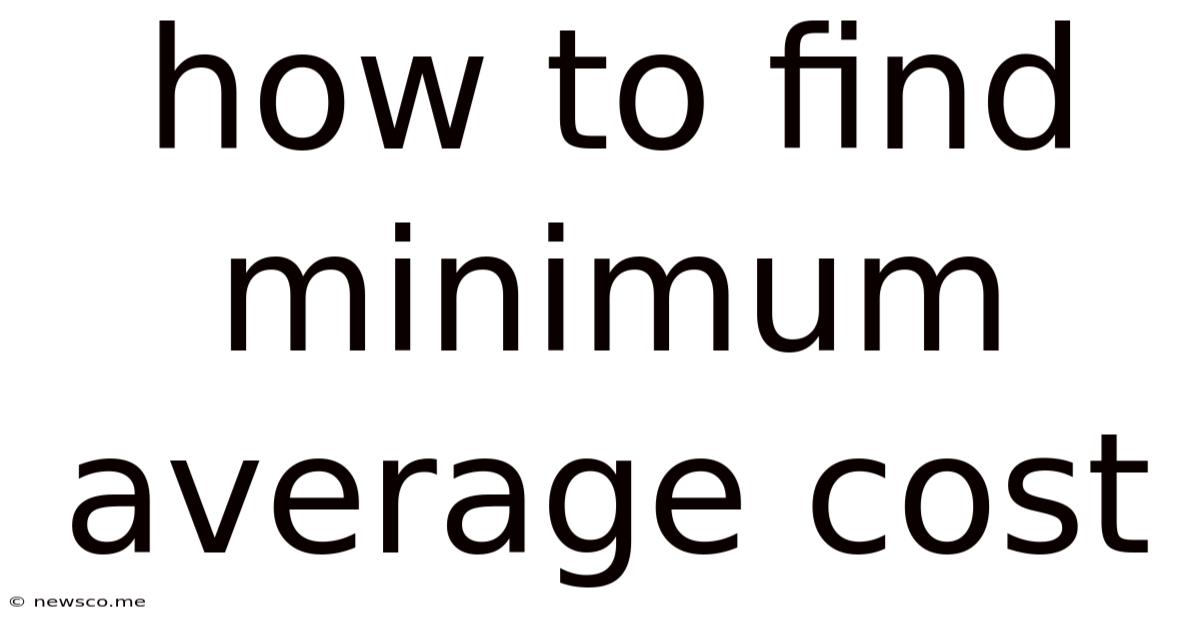
Table of Contents
How to Find Minimum Average Cost: A Comprehensive Guide
Finding the minimum average cost is a crucial concept in economics and business management. Understanding how to determine this point allows businesses to optimize production, maximize profits, and maintain a competitive edge. This comprehensive guide will delve into the theory behind minimum average cost, explore various methods for finding it, and provide practical examples to solidify your understanding.
Understanding Average Cost
Before we tackle finding the minimum, let's establish a clear understanding of average cost itself. Average cost (AC) represents the per-unit cost of production. It's calculated by dividing the total cost (TC) by the quantity of output (Q):
AC = TC / Q
Total cost encompasses both fixed costs (FC) – those that remain constant regardless of production levels (e.g., rent, salaries) – and variable costs (VC) – those that fluctuate with production (e.g., raw materials, labor). Therefore:
TC = FC + VC
Consequently, average cost can also be broken down into:
AC = AFC + AVC
Where:
- AFC (Average Fixed Cost) = FC / Q
- AVC (Average Variable Cost) = VC / Q
Identifying the Minimum Average Cost
The minimum average cost (min AC) is the lowest point on the average cost curve. This point represents the most efficient level of production, where the firm produces each unit at the lowest possible average cost. Finding this point is critical for profit maximization. Producing below this point leads to higher average costs due to underutilized capacity, while producing above it leads to diminishing returns and increased average costs.
Several methods can be used to find the minimum average cost, depending on the information available:
1. Graphical Method
This is the most intuitive approach. By plotting the average cost curve (AC) against the quantity of output (Q), you can visually identify the lowest point on the curve. This point corresponds to the minimum average cost. This method is straightforward for visualizing the relationship, but relies on accurate data and plotting. Inaccuracies in data collection or plotting can lead to an inaccurate representation of the minimum average cost.
2. Analytical Method (Calculus)
This method utilizes calculus to find the minimum point of the average cost function. It involves taking the derivative of the average cost function with respect to quantity (Q), setting it equal to zero, and solving for Q. This Q value represents the quantity at which the average cost is minimized. The second derivative test can confirm whether this point is indeed a minimum. This method requires a precise mathematical representation of the cost function. Estimating the function incorrectly will yield inaccurate results.
Steps:
- Formulate the Average Cost Function: Express the average cost (AC) as a function of quantity (Q) using the total cost function.
- Find the First Derivative: Differentiate the AC function with respect to Q (dAC/dQ).
- Set the First Derivative to Zero: Solve the equation dAC/dQ = 0 for Q. The solutions represent potential minimum or maximum points.
- Find the Second Derivative: Differentiate the first derivative with respect to Q (d²AC/dQ²).
- Second Derivative Test: If the second derivative (d²AC/dQ²) is positive at the value of Q found in step 3, it indicates a minimum. If negative, it indicates a maximum.
3. Numerical Method (Iteration)
This method is useful when the average cost function is complex or not easily differentiable. It involves systematically trying different quantities of output to find the quantity that yields the lowest average cost. This could be done through spreadsheet software like Excel or more sophisticated numerical analysis techniques. While not as precise as calculus, it provides a practical approach when dealing with complex cost structures or limited data. The accuracy of this method depends on the granularity of the tested quantities.
4. Using Data Analysis Software
Statistical software packages (like SPSS, R, or Stata) can be used to fit a suitable function (e.g., polynomial, exponential) to the observed average cost data. Once a suitable function is fitted, the software can be used to find the minimum of this function, providing both the minimum average cost and the corresponding quantity. The accuracy depends on the suitability of the fitted model.
Practical Examples
Let's illustrate these methods with examples:
Example 1: Graphical Method
Imagine a company has the following average cost data:
Quantity (Q) | Average Cost (AC) |
---|---|
10 | $25 |
20 | $20 |
30 | $18 |
40 | $19 |
50 | $22 |
Plotting this data on a graph would show that the minimum average cost is $18, achieved at a quantity of 30 units.
Example 2: Analytical Method (Calculus)
Let's assume a company has the following total cost function:
TC = 100 + 10Q + 0.1Q²
The average cost function is:
AC = TC/Q = 100/Q + 10 + 0.1Q
To find the minimum, we take the first derivative:
dAC/dQ = -100/Q² + 0.1
Setting it to zero:
-100/Q² + 0.1 = 0
Solving for Q:
Q² = 1000
Q = 31.62 (approximately)
To confirm it's a minimum, we take the second derivative:
d²AC/dQ² = 200/Q³
At Q = 31.62, the second derivative is positive, confirming a minimum. Substituting Q back into the AC function gives the minimum average cost.
Example 3: Numerical Method
Suppose we have a more complex cost function which is difficult to differentiate, or we only have discrete data points. We can use a spreadsheet program to calculate average cost for different values of Q and find the minimum value through observation.
Factors Affecting Minimum Average Cost
Several factors influence the location and value of the minimum average cost:
- Economies of Scale: As production increases, average costs often decline due to factors like specialization, bulk purchasing, and efficient use of resources. This contributes to a lower minimum average cost.
- Diseconomies of Scale: Beyond a certain point, increasing production can lead to higher average costs due to managerial inefficiencies, communication breakdowns, and coordination difficulties.
- Technology: Technological advancements can reduce production costs and shift the average cost curve downward, leading to a lower minimum average cost.
- Input Prices: Fluctuations in the prices of raw materials, labor, and other inputs directly impact the average cost curve and its minimum point.
- Production Efficiency: Improved management practices, efficient processes, and skilled labor can significantly lower average costs and shift the minimum point.
Conclusion
Finding the minimum average cost is a fundamental task for any business striving for efficiency and profitability. While the graphical method provides a visual understanding, the analytical and numerical approaches offer more precise calculations, especially when dealing with complex cost structures. Understanding the factors that influence minimum average cost allows businesses to make informed decisions about production levels, pricing strategies, and investment in technology and efficiency improvements. By mastering these concepts, businesses can achieve optimal production levels, minimize costs, and maximize their chances of long-term success.
Latest Posts
Latest Posts
-
An Angle With A Measure Of 180
May 08, 2025
-
What Are All The Math Properties
May 08, 2025
-
How Many Zeros Are In 3 Million
May 08, 2025
-
Which Expressions Represent The Product Of Exactly Two Factors
May 08, 2025
-
How Long Is 5 8 Of An Inch
May 08, 2025
Related Post
Thank you for visiting our website which covers about How To Find Minimum Average Cost . We hope the information provided has been useful to you. Feel free to contact us if you have any questions or need further assistance. See you next time and don't miss to bookmark.